- Research areas : /en/applied-research/iprint/research-areas/
- Inkjet Training Center : /en/applied-research/iprint/inkjet-training-center/
- How to work with us : /en/applied-research/iprint/how-to-work-with-us/
- Digital manufacturing : /en/applied-research/iprint/digital-manufacturing/
- Project portfolio : /en/applied-research/iprint/project-portfolio/
- Equipment : /en/applied-research/iprint/equipment/
- Publications : /en/applied-research/iprint/publications/
- About us : /en/applied-research/iprint/about-us/
- Research areas : /en/applied-research/iprint/research-areas/
- Inkjet Training Center : /en/applied-research/iprint/inkjet-training-center/
- How to work with us : /en/applied-research/iprint/how-to-work-with-us/
- Digital manufacturing : /en/applied-research/iprint/digital-manufacturing/
- Project portfolio : /en/applied-research/iprint/project-portfolio/
- Equipment : /en/applied-research/iprint/equipment/
- Publications : /en/applied-research/iprint/publications/
- About us : /en/applied-research/iprint/about-us/
ComplexFluidPrint
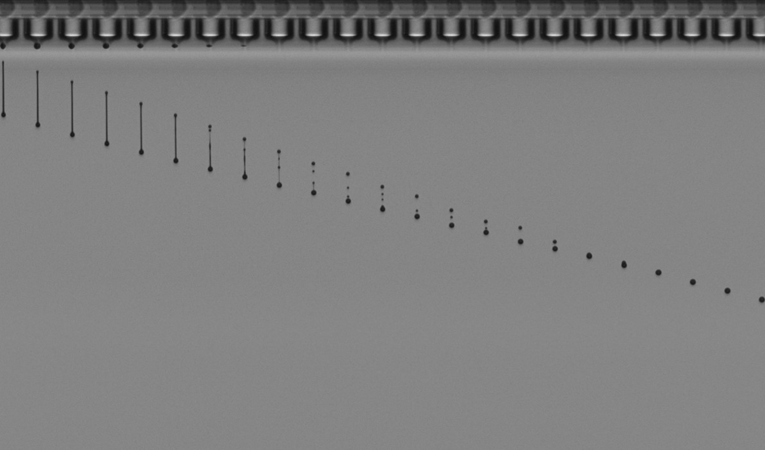
An industrial piezo-electric drop-on-demand print head has been modified to increase the printable viscosity and the droplet speed to reach longer distances.
For this purpose, a new micromanufacturing technology has been employed to directly engrave new microchannels designs and nozzle geometries in a monolith of glass, with a sub-micron precision. A new simple yet robust assembly method has been developed to connect the glass microfluidic device to the actuators’ module. Fluids with a much higher viscosity than the recommended one could be jetted. The jetting speed could be doubled, while keeping an excellent droplet formation mechanism. The micromanufacturing technology employed and the assembly process developed open the door to the development of new print head designs.