- Research areas : /fr/recherche-appliquee/iprint/research-areas/
- Inkjet Training Center : /fr/recherche-appliquee/iprint/inkjet-training-center/
- How to work with us : /fr/recherche-appliquee/iprint/how-to-work-with-us/
- Digital manufacturing : /fr/recherche-appliquee/iprint/digital-manufacturing/
- Project portfolio : /fr/recherche-appliquee/iprint/project-portfolio/
- Equipment : /fr/recherche-appliquee/iprint/equipment/
- Publications : /fr/recherche-appliquee/iprint/publications/
- About us : /fr/recherche-appliquee/iprint/about-us/
- Research areas : /fr/recherche-appliquee/iprint/research-areas/
- Inkjet Training Center : /fr/recherche-appliquee/iprint/inkjet-training-center/
- How to work with us : /fr/recherche-appliquee/iprint/how-to-work-with-us/
- Digital manufacturing : /fr/recherche-appliquee/iprint/digital-manufacturing/
- Project portfolio : /fr/recherche-appliquee/iprint/project-portfolio/
- Equipment : /fr/recherche-appliquee/iprint/equipment/
- Publications : /fr/recherche-appliquee/iprint/publications/
- About us : /fr/recherche-appliquee/iprint/about-us/
Digital manufacturing
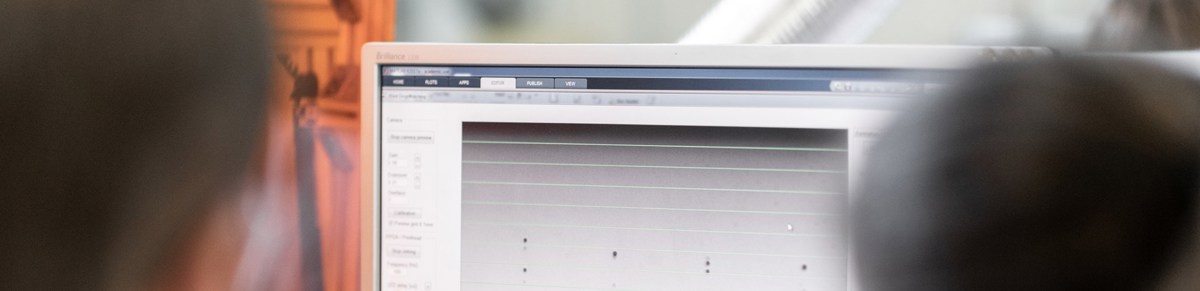
Digital production can be employed in a variety of domains where it replaces analog printing. Its successful implementation mainly depends on the formulation of a suitable functional ink and the availability of compatible printing and pre- or post-treatment technologies. These are precisely iPrint’s areas of expertise.
And when these technologies are not yet available, iPrint is fully capable of developing them. We can support our partners through each process step described below, but also develop entirely new technologies to enlarge the potential of digital production.
Material
At iPrint, we develop digital printing processes with a plethora of different materials: pigments, silver, copper, gold or ceramic nanoparticles, graphene flakes, CNT, cells, proteins and photonic balls, to give just a few examples. UV, solvent, water, oil-based or even e-beam inks are used on a daily basis. Depending on the customer application requirements, existing inks can directly be used or new ones can be formulated.
iPrint can count on very strong partnerships with ink manufacturers worldwide that give us access to the most suitable materials and enable us to develop high-value products. Furthermore, we collaborate with top-notch universities to develop innovative materials for future applications. It is worth mentioning that iPrint is also working with materials that can be deposited with other digital printing technologies, such as direct ink writing, extrusion or FDM.
Ink characterization
The first step towards an inkjet-based digital production is material characterization. iPrint is fully equipped to carry out accurate analysis of the physico-chemical and rheological properties of the inks and substrates.
Surface and interfacial tensions can be measured to ensure the right balance between polar and disperse parts and therefore the desired wetting and adhesion of an ink on a substrate. Dynamic surface tension analysis is key to investigating the surface tension at short surface ages and therefore to obtaining the most suitable surfactant, for example.
Regarding rheological measurements, we work in very close collaboration with our external research associate, Dr. Tri Tulardhar. The TriPAV allows us to measure complex viscosity at high frequencies and at different temperatures, which is key to optimizing the ink formulation and to finding the potentially most suitable jetting temperature. The TriMaster, on the other hand, allows us to characterize the visco-elastic behaviour of an ink and to optimize its formulation to avoid a too Newtonian behaviour, which might result in many satellites or in a too visco-elastic behaviour preventing the ligament breakup. Ink stability and compatibility tests as well as particle-size characterization complete our offer.
Pre-treatments
Depending on the physico-chemical properties of the ink and substrate, as well as on the desired contact angle, a pre-treatment step might be necessary prior to printing. At iPrint, our platforms are equipped with most of the industry-standard technologies, including plasma, corona or flame treatments. Primers can be employed as well. We are also working on new digital pre-treatment technologies.
Printing
The heart of the process is material deposition. iPrint has unique expertise in inkjet printing thanks to more than a decade of research activities, and the hiring of worldwide experts in this field. One of the strengths of iPrint is the availability of print heads and electronics from most of the leading manufacturers. Depending on customer and process needs, we will select the most suitable print head and electronics.
iPrint is currently also in charge of testing new print heads that are not yet on the market. We are always one step ahead and can provide support for the best selection of print head and electronics. This is of course also true for customers working with binder jetting technology, where new print heads can unlock the hidden potential of this booming technology.
iPrint is also developing strong competencies in hybrid advanced manufacturing processes combining different printing technologies, such as inkjet, direct ink writing, extrusion or FDM to overcome the limitations of each technology and allow new products to be digitally manufactured.
Post-treatment
iPrint is equipped with the necessary devices to post-treat printed layers and also possesses significant know-how in this process step. Depending on the ink, treatments such as UV, NIR, IR, photonic, e-beam or just ovens can be used to cure, dry or sinter the layers. Combining different post-treatment steps to treat multimaterials is also a competence available at iPrint. Several lamps are available and can be mounted on our versatile research printer platforms.
Platforms
Over the past years, iPrint has built more than 50 research platforms. Such platforms are very modular and can be modified for the specific need of a given process. Furthermore, a single printer can accommodate multiple inkjet print heads and pre-/post-treatment devices. New hybrid platforms combining several printing deposition methods have also been developed. iPrint’s facilities include 6-axis robotic arms for direct-to-shape applications, and a technology for this domain is currently in development. It is important to mention that strong competencies in ink systems are available at iPrint. Finally, all of our platforms are equipped with drop watching stations to directly optimize the waveform on the printer.
It has to be stressed that iPrint printing platforms are research platforms not suitable for industrial production. Once the process has been developed at iPrint, we can work in close collaboration with machine integrators to create an industrial machine for our clients using processes and equipment developed and selected by iPrint.
Products
The digital printing processes developed by iPrint can be applied in a variety of application domains.
Examples are:
- Biomedical & health
- Automotive & transportation
- Chemistry & materials
- Earth & space
- Electronics & automation
- Fashion & design
- Manufacturing & construction
- Energy & environment.
Our strong expertise in inkjet enables us to identify and deliver innovative solutions for our clients.